The main differences between Centrifugal pumps and Positive Displacement pumps
- March 12, 2014
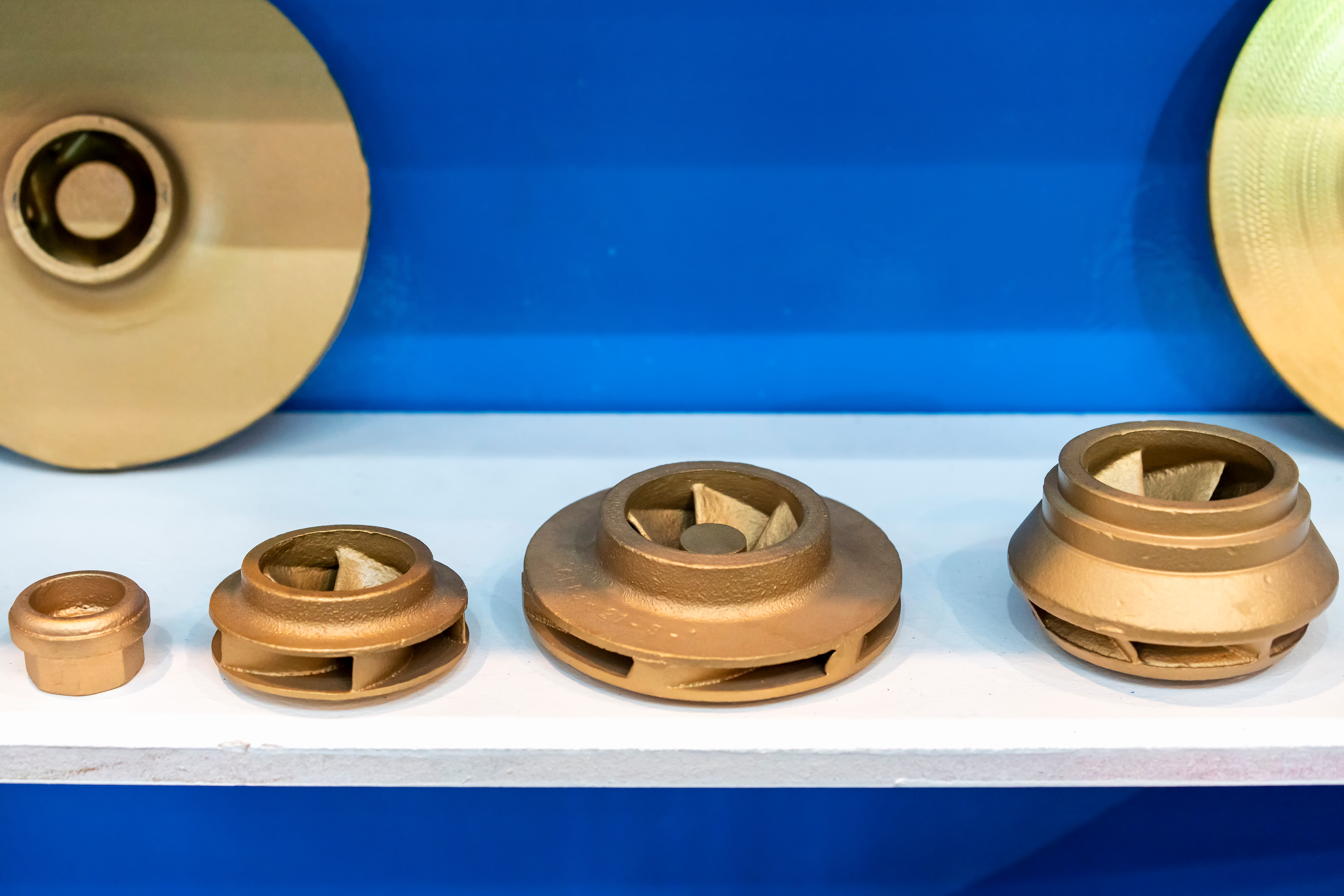
Depending on the task you have at hand, you’ll likely be making a decision between using a centrifugal pump and a positive displacement pump. If you’ve never used an industrial pump before, or if you’re just uncertain as to which pump would be best for your needs, this short guide on the differences between centrifugal and positive displacement pumps should help you.
The easiest way to classify the differences between both of these types of pump is to define each one. First of all, let’s take a look at centrifugal pumps.
What are centrifugal pumps?
Centrifugal pumps operate by converting power into kinetic energy. Fluid enters the pump and is accelerated by the pump’s impeller – moving radially outward. During this process, a vacuum is created that allows for more fluid to be continually drawn into the pump, this helps to increase pressure and forces fluid out of the pump discharge.
These types of pump are used very widely across industry, with the ‘radial flow centrifugal pump’ (as described above) being the most popular pump flow pattern.
Centrifugal pumps can also work on an axial flow system – which draws fluid in along the axis and moves it out along the axis at the opposite side of the pump.
What are the main uses of a centrifugal pump?
As mentioned, centrifugal pumps are arguably the most widely used pump in industry. Their uses vary depending on the size of the pump/the job at hand. However, here’s an idea of the sort of tasks centrifugal pumps can help with:
- Circulating water and other thin liquids (circulator pumps)
- Removing corrosive liquids from narrow-entrance drums (drum pumps)
- Pumping chemicals that are difficult to seal (canned motor pumps)
- Draining sewage and other wastewater (grinder pumps)
- Pumping small amounts of water in wells (jet pumps)
- Handling large solids while dewatering a given area (trash pumps)
What are positive displacement pumps?
Positive displacement pumps work a little differently to their centrifugal counterparts. This type of pump forces a measured quantity of fluid from the pump inlet towards the pump discharge during each pump cycle. This leads to a pulsating flow; which results in periods of fluid exiting the pump followed by periods of no fluid exiting the pump.
The pump itself has an expanding cavity on the entry side and a decreasing cavity on the exit side, which helps to regulate the constant delivery of each cycle of operation.
One of the main differences between positive displacement pumps and centrifugal pumps is that displacement pumps produce the same fluid flow at a set speed – no matter what the discharge pressure is. As well as this, a positive discharge pump cannot be operated against a closed valve (it will just result in damage/line breakage); whereas a centrifugal pump will only build up to the maximum pressure of the pump and most likely cut off (depending on the type of centrifugal pump).
There are often three classifications of positive displacement pump, these are:
- Rotary pumps
- Reciprocating pumps
- Diaphragm pumps
What are the main uses of a positive displacement pump?
While positive displacement pumps can be used to move liquids, they tend to be chosen for more specific tasks – involving high pressure, for example, or suction lift applications.
Here’s an idea of the sort of tasks these pumps can help with:
- Moving concrete long distances as well as upwards during pouring (concrete pumps)
- Moving liquids containing solids – where the pump may be required to run dry (diaphragm pumps)
- Moving thick and corrosive liquids – where the pump flow needs to be controlled/adapted (metering pumps)
- Moving thin liquids such as water – where a slower speed pump is required (piston pumps)
So, there you have a brief guide to the differences between positive displacement and centrifugal pumps. Of course, we recommend you take a little longer to research into the type of pump you may require for your needs.